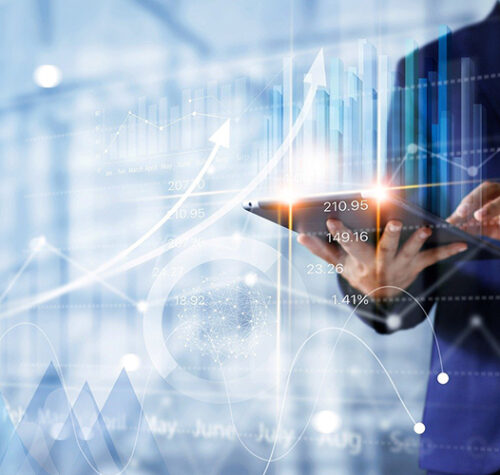
Key ERP Functions Every Small & Medium Enterprises Needs to Succeed
Running a small or medium-sized enterprise (SME) comes with unique challenges—balancing budgets, managing growth and staying competitive. That’s where an ERP (Enterprise Resource Planning) system steps in. But what functions should your ERP system have to truly make an impact? Let’s explore the must-have features that can take your business to the next level.
Accounting and Financial Management
Keeping your finances in check is crucial. ERP systems simplify accounting tasks by providing tools for accurate bookkeeping and comprehensive financial reporting. For instance, N&N Moving Supplies, a family-run distributor, implemented an ERP system that reduced payroll processing time by 84% and improved financial accuracy across its locations. This transparency not only helps in compliance with regulations but also aids in avoiding costly errors.
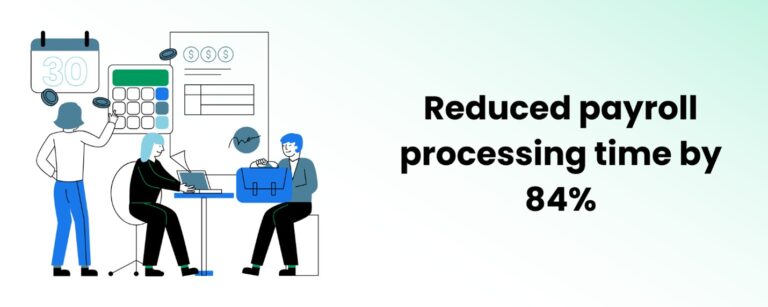
Inventory Management
No more overstocking or stockouts. With ERP, you can monitor inventory levels in real time, ensuring you always have the right products available. This reduces waste while saving money and keeps your customers happy.
Sales and CRM (Customer Relationship Management)
Customer satisfaction is a key driver of growth. ERP systems facilitate the tracking of sales activities and management of customer relationships, consolidating all client data in one place. This integration enables businesses to close deals more effectively and build lasting relationships. Companies leveraging these systems have reported improved customer engagement and higher sales conversion rates due to better access to customer insights.
Supply Chain Management
A strong supply chain management keeps your business running. From coordinating with vendors to tracking shipments, an ERP streamlines your supply chain. You can automate purchase orders and track vendor performance. This ensures timely deliveries, reduces costs, and keeps your operations efficient.
Integration with Other Application
Your ERP System shouldn’t work in isolation. An effective ERP system should integrate seamlessly with other tools such as payroll systems and project management software. This connectivity reduces manual data entry and enhances workflow efficiency. For example, integrating HR modules with payroll software can automate salary calculations and track employee performance, allowing HR teams to focus on strategic initiatives rather than administrative tasks.
Reporting and Analytics
Making the right business decisions starts with having the right data. ERP systems provide dashboards and real-time insights into operations, helping SMEs identify trends and opportunities swiftly. The ability to analyze data effectively can lead to informed strategic decisions that drive business success. Research indicates that companies using ERP solutions see a reduction in decision-making time by over 35% due to improved data visibility.
Summary
Implementing an ERP system can be a game-changer for SMEs looking to streamline operations and enhance customer experiences. With essential functions like accounting management, supply chain optimization, integration features, and robust analytics, ERP systems equip businesses with the tools necessary to thrive in a competitive landscape. By embracing these technologies, SMEs can turn challenges into opportunities for growth and success in today’s dynamic market environment.