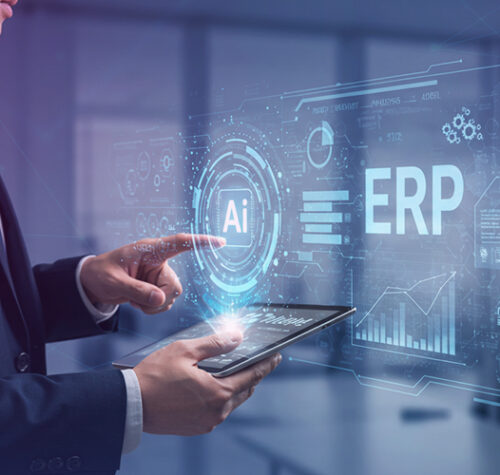
ERP with AI: The Future of Enterprise Resource Planning
The integration of Artificial Intelligence (AI) with Enterprise Resource Planning (ERP) systems is transforming how organizations manage their resources, make decisions, and gain competitive advantages. This powerful combination is not just a technological upgrade-it’s a fundamental shift in how businesses operate and strategize for the future.
Current Applications of AI in ERP
The marriage of AI and ERP has already yielded impressive results across various business functions. Let’s explore the key technologies driving this transformation:
Machine Learning for Predictive Analytics
Machine Learning algorithms are revolutionizing ERP systems by analyzing historical data to identify patterns and trends that would be impossible for humans to detect manually. These AI-powered ERP solutions leverage advanced algorithms to anticipate future trends, identify potential risks, and recommend optimal courses of action. Whether predicting inventory needs or forecasting sales, ML-driven ERP systems provide businesses with the insights needed to make proactive rather than reactive decisions.
Modern ERP systems utilize ML, data mining, and predictive analytics to process vast amounts of information, enabling businesses to make smarter decisions based on data-driven intelligence rather than guesswork. For manufacturers, this means more accurate demand forecasting, optimized production schedules, and improved resource allocation.
Natural Language Processing for Streamlined Communication
Natural Language Processing (NLP) capabilities are enhancing how users interact with ERP systems. AI-powered chatbots and virtual assistants enable employees to query company data, generate reports, and perform complex tasks using conversational language rather than learning specific system commands or navigation paths.
This technology democratizes access to data across organizations, allowing non-technical staff to extract valuable insights without specialized training. When an inventory manager can simply ask, “What products are running low this month?” and receive an accurate response, the efficiency gains are substantial.
Robotic Process Automation for Operational Efficiency
Robotic Process Automation (RPA) is eliminating repetitive, manual tasks that have traditionally consumed valuable human resources. Modern autonomous ERP systems integrate RPA to create self-managing, self-optimizing, and self-healing systems that minimize human intervention in routine processes.
Tasks such as data entry, invoice processing, and inventory management can now be automated, reducing human errors and increasing efficiency. This automation frees employees to focus on more strategic, value-added activities that require human creativity and problem-solving skills. In manufacturing environments, this translates to increased throughput and enables innovation and continuous improvement processes.
Image Processing for Advanced Quality Control
One of the most impressive applications of AI in ERP is in quality control through advanced image processing and computer vision. In manufacturing settings, AI-powered visual inspection systems can detect product defects, ensure proper packaging, and verify product specifications with unprecedented accuracy and speed.
These systems follow a systematic process that includes image capture, processing, comparison against quality standards, and automated decision-making. For example, computer vision can inspect labels on bottles or containers to ensure they are correctly applied, legible, and match the product inside. This technology has made quality control more reliable while significantly reducing the cost of inspections.
In production line monitoring, advanced statistical quality control techniques using image intelligence help analyze complex image data streams, detecting shifts in quality and identifying faulty regions with remarkable precision.
The Next Wave of AI in Enterprise Resource Planning
As impressive as current AI applications in ERP are, the next generation promises even greater transformations:
Autonomous Decision-Making Systems
The concept of autonomous ERP represents a quantum leap from traditional systems. These advanced platforms minimize human intervention not just in routine tasks but in complex decision-making processes as well. Autonomous ERP systems continuously monitor and analyze business processes, identifying inefficiencies and implementing improvements without requiring human intervention.
This self-optimizing capability leads to increased productivity and cost savings by automatically adjusting processes based on changing conditions. For example, an autonomous ERP might automatically adjust production schedules when it detects supply chain disruptions or changes in customer demand patterns.
AI-Powered Scenario Planning and Forecasting
The next generation of ERP systems will excel at scenario planning and forecasting, giving businesses unprecedented ability to prepare for multiple future scenarios. AI-based predictive analytics are already transforming demand forecasting in ERP systems by synthesizing and analyzing vast datasets to identify patterns invisible to human analysts.
Future systems will take this further by simultaneously modeling multiple business scenarios and recommending optimal strategies for each. Rather than simply predicting what might happen, these systems will advise on what should be done in response to changing conditions.
Deep Integration with IoT and Real-Time Analytics
Real-time data processing represents another frontier for AI-powered ERP. Modern systems excel at consistently evaluating and interpreting extensive operational data, enabling manufacturers to make informed decisions without delay.
Instead of relying on end-of-day reports, AI-driven ERPs provide live dashboards that monitor production metrics, inventory levels, and quality control indicators. Decision-makers can immediately adjust production schedules or reallocate resources based on current conditions, driving greater efficiency and agility in dynamic markets.
Why Businesses Should Prepare for AI in Enterprise Resource Planning
The transition to AI-powered ERP isn’t just about staying current with technology-it’s about business survival and growth in an increasingly competitive landscape.
Enhanced Productivity and Innovation
AI-driven automation increases productivity by handling routine tasks with greater speed and accuracy than human workers. This automation enables human resources to focus on more strategic, high-value activities, fostering innovation and continuous improvement in business processes.
When employees are freed from data entry, report generation, and other routine administrative tasks, they can devote more energy to creative problem-solving, strategic planning, and customer relationship management-activities where human intelligence still far surpasses artificial intelligence.
Competitive Advantage in a Rapidly Evolving Market
Companies that implement AI-driven ERP solutions gain a significant competitive edge. These early adopters can deliver results faster and more accurately while responding to changing market requirements much quicker than competitors using traditional systems.
In today’s fast-paced business environment, the ability to quickly adapt to market changes, customer preferences, and supply chain disruptions is often the difference between market leaders and followers. AI-powered ERP systems provide the agility needed to thrive in uncertain conditions.
Conclusion
The integration of AI with ERP represents a paradigm shift in how businesses manage their operations and make decisions. From machine learning and natural language processing to robotic process automation and image intelligence, these technologies are already delivering substantial benefits to early adopters.
As we look toward the future of autonomous decision-making, advanced forecasting, and real-time analytics integration, it’s clear that AI-powered ERP will be a cornerstone of successful businesses. Organizations that embrace these technologies now will be better positioned to enhance productivity, foster innovation, and maintain competitive advantage in increasingly challenging markets.
The question is no longer whether businesses should adopt AI-powered ERP, but how quickly can they implement these systems to avoid being left behind in the next wave of digital transformation.